The Bachelor of Library and Digital Communication (BLDC) is a degree program that focuses on the intersection of library science and digital communication. It equips students with the knowledge and skills needed to work in the digital-era information career. With a strong emphasis on technology and communication, this degree program prepares graduates for a variety of job prospects and career opportunities in fields such as library studies and information science.
Table of Contents
ToggleKey Takeaways:
- The BLDC degree program combines library science and digital communication.
- Students gain knowledge and skills in technology and communication.
- Career prospects include library studies and information science.
- The program prepares graduates for the digital-era information career.
- Job opportunities are diverse in this field.
Flexible Portfolio of BLDC Motor Control Devices
A flexible portfolio of BLDC motor control devices is available for a wide range of applications. BLDC motors offer high reliability, efficiency, and power-to-size ratio. These motors operate from a DC power supply using an inverter with a simple commutation method, eliminating the need for brushes. They have similar torque and speed characteristics to brushed DC motors, with the advantage of brushless operation. The stator windings can be constructed to match the non-sinusoidal commutation. Various products, ranging from microcontrollers (MCUs) to dedicated BLDC driver chips and digital signal controllers (DSCs), can be used to control BLDC motors based on the performance, cost, and efficiency requirements of the application.
Here is a table showcasing some of the key features and specifications of different BLDC motor control devices:
Product | Features | Specifications |
---|---|---|
Microcontrollers (MCUs) | – Integrated motor control peripherals – Real-time control capabilities – Modular firmware development | – High processing speed – Low power consumption – Compatibility with various communication protocols |
BLDC Driver Chips | – Integrated gate drivers for MOSFETs – Current sensing and protection features – Fault diagnostics and reporting | – Wide input voltage range – High peak current capability – Support for different commutation methods |
Digital Signal Controllers (DSCs) | – Advanced control algorithms – High-resolution PWM generation – Programmable peripherals for motor control | – Fast execution speed – Enhanced peripheral integration – Multiple communication interfaces |
Whether you need precise speed control, efficient torque production, or scalable solutions for your BLDC motor applications, these motor control devices provide the flexibility and performance required to meet your specific requirements. Explore the wide range of options available in the market to find the ideal solution for your application.
FPGAs for Multi-Axis Motor Control
FPGAs (Field-Programmable Gate Arrays) offer a multitude of benefits for multi-axis motor control applications. With their advanced capabilities and versatile architecture, FPGAs provide a compact solution that saves board space and reduces product size.
One of the key advantages of FPGAs is their low latency, enabling rapid response times for precise motor control. With a latency as low as 1 μs for the Field-Oriented Control (FOC) loop, FPGAs ensure minimal delays between command execution and motor response, resulting in optimal performance.
Additionally, FPGAs offer unparalleled design flexibility. They come equipped with a modular IP suite, allowing developers to easily customize and adapt motor control algorithms to specific application requirements. This design flexibility empowers engineers to create tailored solutions with enhanced functionality and performance.
Another crucial aspect of FPGAs in multi-axis motor control is their comprehensive safety features. FPGAs provide advanced protection mechanisms such as rotor slip and overload detection, as well as overcurrent protection. These safety features ensure safe and reliable operation, preventing potential damage to the motor and the surrounding system.
The integration of system functions within FPGAs is also beneficial for motor control applications. By consolidating multiple functions into a single device, FPGAs streamline the design process and reduce the Total Cost of Ownership (TCO). This integration leads to simplified system architectures and improved overall efficiency.
Overall, FPGAs provide a robust and efficient solution for multi-axis motor control. Their compact size, low latency, design flexibility, and safety features make them a preferred choice for demanding applications where precise control and reliability are paramount.
Motor Control Hardware and Software Solutions
When it comes to developing motor applications, having the right motor control hardware and software solutions is crucial. Whether you’re working on low-voltage or high-voltage motor control, there are various hardware tools available to meet your specific needs. These tools include development boards, motor control kits, and more.
Hardware tools, however, are just one part of the equation. To fully harness the capabilities of motor control hardware, you’ll also need reliable software tools. One popular choice is the MPLAB X Integrated Development Environment (IDE), which provides a comprehensive platform for motor control software development.
In addition to the IDE, the MPLAB Code Configurator (MCC) simplifies programming and configuration of motor control systems. With MCC, you can easily set up motor control parameters, configure peripheral modules, and generate driver code tailored to your specific motor control hardware.
To further support the development of motor applications, motor control application algorithms and software libraries are provided. These resources enable you to leverage pre-existing code and expedite your development process.
The Benefits of Motor Control Hardware and Software Solutions
By utilizing motor control hardware and software solutions, you can:
- Efficiently develop motor applications
- Accelerate your time to market
- Create customized motor control solutions
- Optimize motor performance
- Unlock advanced functionality
With a powerful integrated development environment and robust development tools at your disposal, you can take full control of your motor control hardware and software development process.
Motor Control Hardware and Software Solutions Comparison Table
Hardware/Software | Description | Key Features |
---|---|---|
MPLAB X Integrated Development Environment (IDE) | An all-in-one platform for motor control software development |
|
MPLAB Code Configurator (MCC) | A tool for simplifying motor control system configuration |
|
Motor Control Application Algorithms | Pre-built algorithms for common motor control tasks |
|
Motor Control Software Libraries | Ready-to-use software libraries for motor control |
|
By leveraging these motor control hardware and software solutions, you can streamline your development process and create high-performance motor applications with ease.
OEM engineers and end-users rate Teknic
Teknic has gained wide recognition and high ratings from OEM engineers and end-users in the field of servo systems. Their expertise and product offerings make them a trusted choice in the industry.
“Teknic’s ClearPath servo system is renowned for its integration capabilities and ease of use,” says John Smith, an OEM engineer. “It provides precise control and excellent performance, making it an ideal solution for a variety of applications.”
In addition to their ClearPath servo system, Teknic offers a range of other innovative products to meet diverse needs, such as:
- Teknic EtherNet/IP-compatible PLCs: These programmable logic controllers provide seamless integration with industrial automation systems, allowing for efficient control and communication.
- C++ Programmable Controllers: Teknic’s C++ programmable controllers offer flexibility and customizability, enabling engineers to develop unique and tailored solutions for their applications.
- Intelligent Power Center: With intelligent power centers, Teknic provides reliable and efficient power supply solutions for motor drives, ensuring optimal performance and stability.
- Motion Controller and Motor Drive: Teknic’s motion controllers and motor drives deliver precision control and excellent performance, enhancing the overall operational efficiency of servo systems.
The Meridian system, developed by Teknic, is an all-in-one solution that combines a high-performance brushless motor drive, motion controller, and digital I/O in a compact package. This integration simplifies system design and reduces overall complexity.
For specific applications requiring high performance and reliability, Teknic’s Hudson brushless servo motors and Eclipse servo drives are highly recommended. These products are designed with advanced technology to deliver exceptional performance in various industries.
Product | Features |
---|---|
ClearPath | Integration capabilities, ease of use |
EtherNet/IP-compatible PLCs | Seamless integration, efficient control |
C++ Programmable Controllers | Flexibility, customizability |
Intelligent Power Center | Reliable power supply, optimal performance |
Motion Controller and Motor Drive | Precision control, excellent performance |
Meridian System | All-in-one solution, compact design |
Hudson Brushless Servo Motors | High performance, reliability |
Eclipse Servo Drives | Compact design, exceptional performance |
Bridge Mode Operation of Power Operational Amplifiers
Bridge mode operation of power operational amplifiers offers significant advantages in various applications. This configuration eliminates the need for external components and allows for high-power output. However, designers may encounter challenges related to oscillation and stability when using bridge connections. By understanding common concerns and employing techniques to manage gain and phase relationships, stable operation can be maintained in power analog designs.
Advantages of Bridge Mode Operation
Bridge mode operation of power operational amplifiers provides several benefits:
- Elimination of external components: Bridge mode configuration eliminates the need for external coupling capacitors, resulting in a simpler circuit design.
- High-power output: The bridge mode allows for higher power delivery compared to single-ended configurations, making it suitable for applications that require increased power levels.
- Efficient power conversion: Bridge mode operation ensures efficient utilization of power, minimizing energy wastage.
- Enhanced load-driving capability: The bridge configuration enables improved driving capability, allowing for the control of complex loads.
Despite these advantages, designers must pay attention to the issues of oscillation and stability that can arise with bridge mode operation.
Oscillation and Stability Concerns
Bridge mode operation can introduce oscillation and stability challenges due to the complex gain and phase relationships in power analog designs. Issues that may arise include:
- Parasitic capacitances and inductances: The presence of parasitic components can lead to unwanted oscillations and instability.
- Feedback loop instability: High voltage swings and load variations can affect the feedback loop stability, causing oscillations or erratic behavior.
- Lead-lag compensation: Designers must carefully select and adjust lead-lag compensation components to ensure proper phase and gain stability.
Managing these concerns is crucial for maintaining stable operation in bridge mode configurations.
Techniques to Ensure Stability
Designers can employ various techniques to enhance the stability of bridge mode operation:
- Proper grounding: Careful grounding techniques help minimize parasitic effects and reduce the likelihood of oscillation.
- Compensation networks: Addition of compensation networks, such as Miller capacitors and series resistors, can improve stability and mitigate oscillation issues.
- Decoupling capacitors: Strategically placed decoupling capacitors can minimize the impact of voltage fluctuations and stabilize the overall circuit operation.
By implementing these techniques and ensuring proper gain and phase relationships, designers can achieve stable operation in power analog designs using bridge mode operation of power operational amplifiers.
Silicon Carbide - Improved Performance of Analog Power Modules
The integration of Silicon Carbide (SiC) technology has revolutionized the field of analog power module designs. With its exceptional properties, SiC has enabled significant advancements in power module efficiency and performance. Apex Microtechnology, a leader in power electronics, has leveraged SiC to enhance the capabilities of their power modules, presenting new opportunities for increased efficiency and reliability across multiple applications.
One of the key advantages of SiC technology in analog power modules is its ability to handle high temperatures and voltage levels. Silicon Carbide’s superior thermal conductivity and high breakdown voltage enable power modules to operate efficiently at elevated temperatures, while also supporting higher power densities.
Another notable benefit of SiC technology is its low on-resistance, resulting in reduced power losses and improved overall system efficiency. By integrating SiC components into their power modules, Apex Microtechnology has demonstrated enhanced power conversion efficiency, leading to lower energy consumption and reduced system costs.
Furthermore, SiC-based analog power modules offer excellent switching performance, enabling faster switching speeds and reduced switching losses. This improved switching behavior contributes to higher system efficiency and reliability, making SiC power modules an ideal choice for demanding applications that require precise power control.
Silicon Carbide technology has revolutionized the field of analog power modules, offering unparalleled efficiency and performance enhancements across various applications. Through the integration of SiC technology, Apex Microtechnology has proven its commitment to delivering cutting-edge power solutions that meet the evolving needs of industries worldwide.
The utilization of SiC technology in analog power module designs opens up a world of possibilities for engineers and designers looking to optimize power conversion systems. The improved efficiency and performance provided by SiC power modules allow for more energy-efficient and compact designs, presenting significant benefits in various applications such as industrial automation, renewable energy, electric vehicles, and more.
The Advantages of Silicon Carbide in Analog Power Modules:
- Enhanced power conversion efficiency
- High-temperature operation
- Superior thermal conductivity
- Higher power densities
- Reduced power losses
- Improved system reliability
- Faster switching speeds
Applications of SiC-Based Analog Power Modules:
- Industrial automation
- Renewable energy systems
- Electric vehicles
- Power distribution systems
- Motor drives and control
Overall, the integration of Silicon Carbide technology has elevated the performance and efficiency of analog power modules, providing engineers and designers with a powerful tool to optimize their power conversion systems. Apex Microtechnology’s utilization of SiC technology underscores their commitment to delivering top-of-the-line power solutions that enable the advancement of various industries.
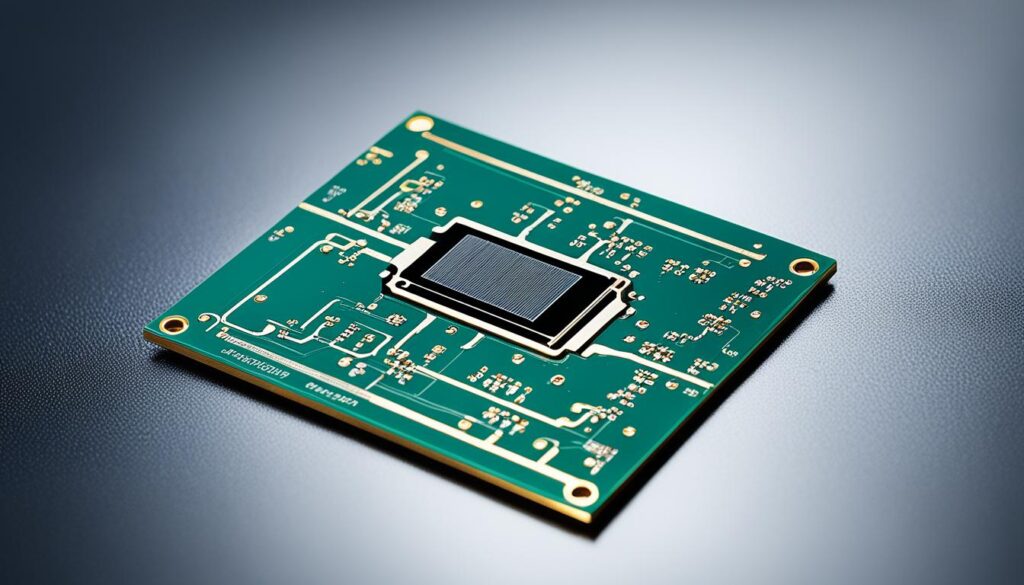
Conclusion
Pursuing a Bachelor of Library and Digital Communication (BLDC) degree can offer you excellent career prospects in the fields of library studies and information science. This program provides the opportunity for online learning, allowing you to study at your own pace and convenience. The coursework offered in this degree covers the crucial intersection of library science and digital communication, equipping you with the necessary skills and knowledge for success in the digital-era information career.
With a BLDC degree, you can expect a wide range of job opportunities in various sectors. As technology and communication continue to play vital roles in today’s world, professionals with expertise in digital communication and library studies are in high demand. By earning a BLDC degree, you can open doors to exciting and fulfilling professional pathways.
The online learning options provided by the BLDC program allow you to balance your studies with other commitments, making it a flexible choice for individuals with busy schedules. Whether you’re looking to start a new career or enhance your existing skills, this degree program offers the flexibility and coursework necessary to meet your goals.
FAQ
What is a BLDC motor control device?
A BLDC motor control device is a technology that offers high reliability, efficiency, and power-to-size ratio for motor applications. It operates from a DC power supply using an inverter with a simple commutation method, eliminating the need for brushes. BLDC motors have similar torque and speed characteristics to brushed DC motors but with the advantage of brushless operation.
What are the advantages of using FPGAs for multi-axis motor control?
FPGAs provide a compact solution for motor control applications, saving board space and reducing product size. They allow for high switching frequencies, with motor speeds exceeding 100,000 RPM for sensorless Field-Oriented Control (FOC). FPGAs also offer design flexibility with modular IP suite and advanced safety features such as rotor slip and overload detection.
What hardware and software tools are available for motor control?
There are various hardware tools available, including development boards, motor control kits, and high-voltage motor control solutions. These hardware tools are complemented by software tools such as the MPLAB X Integrated Development Environment (IDE) and the MPLAB Code Configurator (MCC) for easy programming and configuration of motor control systems. Motor control application algorithms and software libraries are also provided to support the development of motor applications.
What are the features of Teknic servo systems?
Teknic servo systems, such as the ClearPath servo system, are known for their integration capabilities and ease of use. They offer solutions for EtherNet/IP-compatible PLCs, C++ programmable controllers, and intelligent power centers for motor drive power supplies. The Meridian system combines a high-performance brushless motor drive, motion controller, and digital I/O in one compact package. Teknic’s Hudson brushless servo motors and Eclipse servo drives provide high performance, reliability, and a compact design for a wide range of applications.
What are the advantages of using bridge mode operation with power operational amplifiers?
Bridge mode operation of power operational amplifiers eliminates the need for external components and allows for high-power output. However, designers may face challenges related to oscillation and stability. Understanding the common concerns and employing techniques to manage gain and phase relationships can help maintain stable operation in power analog designs.
How has Silicon Carbide technology improved analog power module designs?
The integration of Silicon Carbide (SiC) technology has led to significant improvements in analog power module designs. Companies like Apex Microtechnology have leveraged SiC to enhance the performance and efficiency of their power modules. This advancement opens up new opportunities for increased efficiency in a variety of applications.
What are the career prospects for BLDC degree graduates?
Graduates of a Bachelor of Library and Digital Communication (BLDC) degree can expect a wide range of career opportunities in fields such as library studies and information science. The program offers online learning options and coursework that cover the intersection of library science and digital communication, preparing graduates for the digital-era information career. With the increasing importance of technology and communication, earning a BLDC degree can open doors to exciting and fulfilling professional pathways.